Do you think of starting a manufacturing business after you retire? Well, a manufacturing business can be an attractive idea for your retirement business in Nigeria. The downside, however, is that you might have to spend more money than other businesses initially.
There is the tendency that you will make more money than an agric business because you add value to raw materials. Rather than just growing crops or breeding animals, you produce finished products like packaged tea or organic soap.
Despite the money you spend when you start, it is still easy for the business to fail or underperform. So, you need to get some things right when you start your business.
Here, you will learn three tips to help you set up a profitable manufacturing business after retiring.
Table of contents
- You must understand the production process.
- Comply with regulations in your industry.
- Put a Quality Assurance process in place.
You must understand the production process.
Part of what you should learn before you set up the business is the method of production. While you are not the person doing the work, relying on the knowledge of your workers alone is a recipe for disaster. They can leave the business at any time or sell your trade secret to competitors. That will be a disastrous thing to happen to your business. The Federal Institute of Industrial Research Oshodi (FIRO) offers training on how to make fruit juice, cassava flour, bread and some other products.
The two disastrous things that can happen to your business if you don’t understand the production process are:
a) You will not be able to improve your product.
After some time, your customers will want newer flavors of the product or packaging. If you cannot think of how to meet their needs, they will stop buying from you. Imagine if you are making soap for women and your competitor introduces organic soap to the market. If you don’t know how to produce organic soap, you will undoubtedly lose some customers.
b) Your competitors can easily cripple your business by stealing your workers.
Your competitors can offer your workers higher salaries to come and work for them. If you over-rely on a worker who knows your entire production process, they can offer the information to your competitor. Then, you will be stranded because you cannot quickly train other workers to replace the one who left.
So, before you start manufacturing anything, please spend some time learning how to produce it.
Recommended Reading: 51 businesses you can start with 2 million Naira or less when you retire in Nigeria.
Comply with regulations in your industry.
The second thing you need to do is to comply with the laws in your industry. All businesses are subject to specific regulations within their sectors. An example is if you are in the food and drug sector, your product has to be registered by the National Agency for Food and Drug Administration (NAFDAC).
It might cost you some extra money at the beginning to register your business. However, if your business is certified by regulatory authorities, you will benefit in the following ways:
- Your customers will have confidence that the product is safe to consume. Then, they will continue buying from you.
- Supermarkets and pharmacies can accept your products. That means more customers for you.
Put a Quality Assurance system in place.
The third thing you need to do is to put a quality assurance system in place. A quality assurance system is a system that makes sure that your customers can use your products. It helps you identify and prevent problems before, during, and after production.
It also ensures that your products have the same taste, texture, and size every time you produce.
It starts from making sure that your raw materials are of the highest standard. It ends in the way you deliver the product to your customer.
You have to ensure that the product has no problems affecting its safety or quality at every production stage.
The basic steps for a quality assurance system are:
- A production guide. Your production guide should include the quality of raw material needed for production.
- Conduct market research to find out what your customers want (taste, color, size).
- Check the quality of raw materials you use for production. Contamination can start from there. You should also store raw materials in an appropriate place.
- Create a timetable for cleaning your factory to avoid products getting contaminated. The timetable should be clear about:
- Who should clean each piece of equipment or workspace?
- How often the cleaning should take place.
- What time the area should be cleaned (before and after production).
You can employ a quality assurance officer if you can afford one. If you can’t afford one at the moment, you can attend a course on quality assurance and train your workers yourself. Alternatively, you can also get a consultant to train your staff.
Recommended Reading: Top 3 tips to help you start a retail business when you retire in Nigeria.
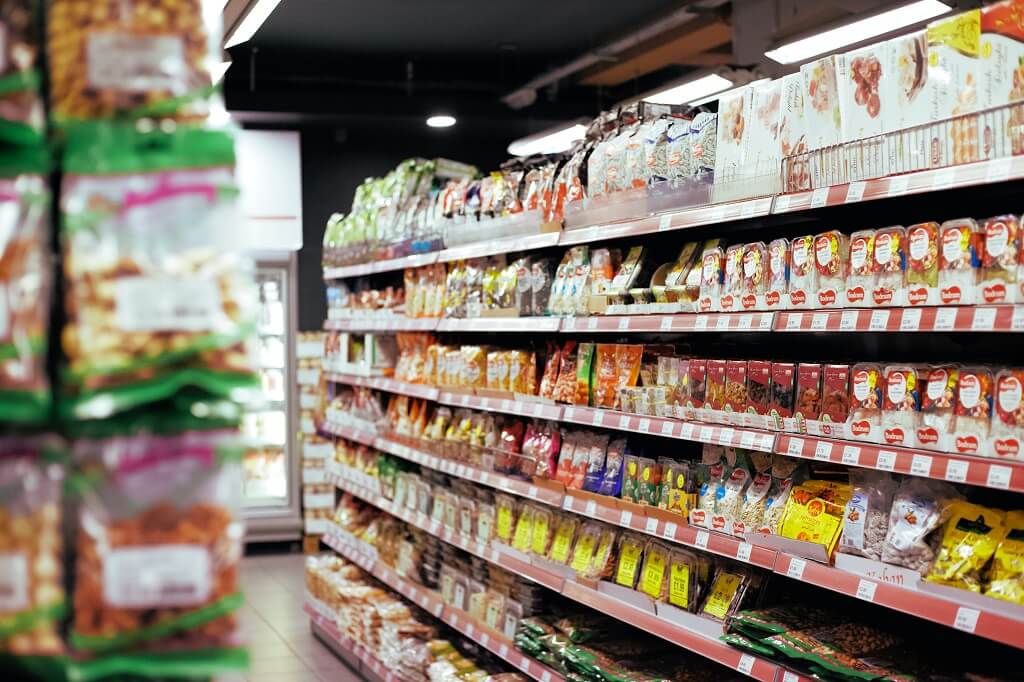
In conclusion
The best way to plan for your manufacturing or agro-processing business is to write a business plan. A plan will help you understand how to operate your business.
You must train your staff. You might not be able to employ the most qualified or experienced workers when you start. So, make sure that you train the ones that you can afford to employ.
It would be best if you also researched the best type of production equipment before buying. You can talk to people in the same industry to find out the best equipment to buy.
Another important aspect of production is supervising the production process. Therefore, you should employ experienced factory supervisors.
Thank you for reading this article to the end. If you learned anything new from this article, please consider subscribing to our email list to get the latest articles. Thank you.